I’ve been busy. But there wasn’t a story to tell until everything was finished. So, this will be another long picture laden post. If you don’t care about the process/samplers, just jump on down to the end to see the finished scarf. Not the scarf, but a pleated scarf nonetheless.
As I said in my last post, I was fixated on Anne Fields’ pleated cashmere scarf. I have some cashmere/silk yarns spun and plied that I thought would be perfect for this project. But, I had only just enough to do one scarf. One shot. No sampling. If it didn’t work, then the yarn is gone.
If that isn’t enough incentive to sample, sample, sample, I don’t know what is.
I had in mind that the contrast stripes would be Crystal Palace Como used here and here. I bought several cones of that from Morgaine back in March, so all is well. Enough to sample. Enough for the project. But what do I use for accent stripes? It needed to be similar size yarn. I auditioned* several but finally settled on Jaggerspun Zephyr.
* Auditioned means that I fondled several. Wound the finalists into balls or onto cones. Fondled some more. Sat and stared at them for a week or so. Carried it around with me. Fondled some more.
The hand wringing included looking up all the weaving books I had that included pleated scarves or pleated projects. (Reference list at the end of the post.) The notes that I had from Anne were the following:
- the structure is 1/3 and 3/1 reverse twill (8 shafts)
- the stripes needed to be less than 1″ for the collapse to happen
- the sett needs to be denser than normal twill
- the weft needs to be finer than the warp (about 8x)
- the beat needs to be more than the sett (about double)
Warp Set Up:
- 19 stripes total of 16 threads per stripe
- 10 stripes of Como (50/50 wool/silk tight spun)
- 9 stripes of Zephyr (50/50 wool/silk softly spun)
- 15 dent reed
- sett: 30 epi
- loom width: 10″
For the weft, I auditioned 4 different yarns:
- ColourMart High Twist Cashmere Single 1/20 NM
- ColourMart Wool/Lycra 2/30 NM
- Handspun Cormo Single (about the same grist as the cashmere single)
- Anne Fields High Twist Wool Single 40/1
I actually wove a baseline using Zephyr, but it did exactly what I expected it to do. Nothing. But what was disappointing was that while some corrugation occurred on some of the samplers when I cut them off the loom, it wasn’t dramatic. After a dunking in a hot bath, they came out flat. I had to coax them into pleats by scrunching them in my hand and lay them to dry.
In the photos below, the top sample is what it looked like off the loom (small sample), the bottom is what they looked like after finishing (and scrunching).

ColourMart Cashmere Single 1/20 NM. 32 ppi.This showed the most pleating straight off of the loom. Not surprisingly, this had the softest hand of all the samples. Due to the cashmere weft, no doubt.
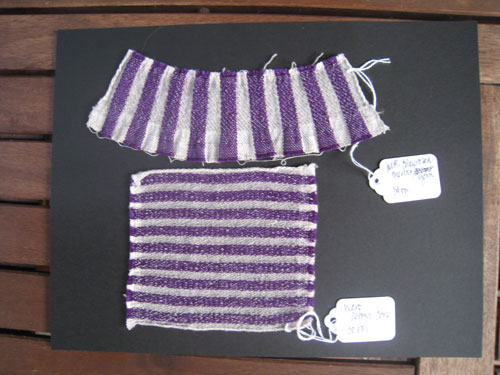
ColourMart Wool/Lycra. 34 ppi. This did what I expected it to do. The lycra pulled it in and overwhelmed the pleating. I did this sample for another project I have in mind,.
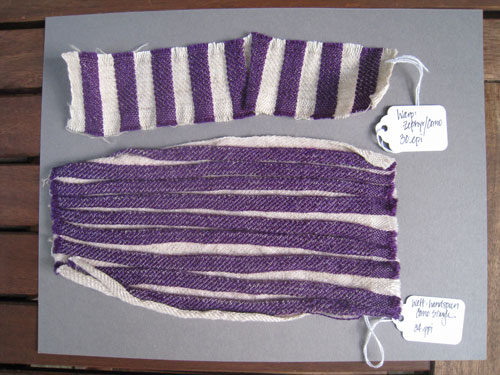
Handspun Cormo Single. 34 ppi. This showed the 2nd most pleating off the loom, but as you can see, it's not much. It curled more though. This also had a pleasing hand.

Anne Field's Hight Twist Single 40/1. 32 ppi This didn't show much pleating at all off loom. This sample felt rough, even after washing. I think it's due to the commercially spun high twist wool.
Things I Learned:
- I knew I wasn’t getting the beats that I should from this project, but I couldn’t beat it any harder. While I was able to get some pleating if I worked the wet fabric, it wasn’t what I expected. I thought that it should “just happen.” Obviously, getting more ppi than epi is the key here.
- It was nice to see that the ColourMart singles and my handspun both worked from the perspective that they showed promise of pleats. This meant that I had a source of fine high twist singles for more collapsed projects. Anne’s 40/1 is impossible to find in the US. Always good to have options. But ColorMart has limited color selections for this. No white nor cream, for example. I used a light grey.
- It was also nice to find that my handspun Cormo worked just as well as the commercial yarn and the hand is almost as nice as the cashmere singles. I have several pounds of this Cormo so I have a steady supply. It takes less than an hour to spin 2 weaving bobbins worth of singles. Each weaving bobbin weaves about 10-15″. The only downside of this is that the cormo is a warm tan color. The options are to dye the wool before spinning (loath to mess up a nice pencil roving from Morro Fleeceworks though!) or look at other wools that I can spin to this grist.
“What about the scarf?” you ask. Well, it’s a pleated scarf, but still not my scarf with the handspun cashmere. Why? I had a birthday present to make and I wanted to sample some more. So…
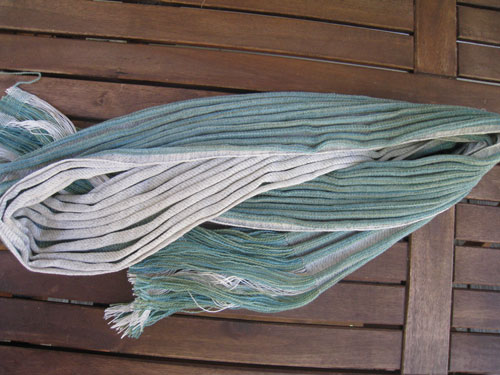
Scarf off of the loom.
The accent stripe is Lisa Souza’s handpainted merino lace, sett at 24 epi. The beat is still 32. While the beat is still not double the epi, it is higher than my samples. And looky what happened! It pleated right up off of the loom. I was so happy that it finally worked.
Why did I choose this yarn? This scarf was destined to be a present to my friend Penny, who gave me the yarn because it wasn’t doing what she wanted. I had wanted to give it back to her in a finished project. Yesterday was her birthday. So it all seemed to make sense. The fact that the scarf pleated up upon removal from the loom was a HUGE bonus. I didn’t have to manipulate it at all.
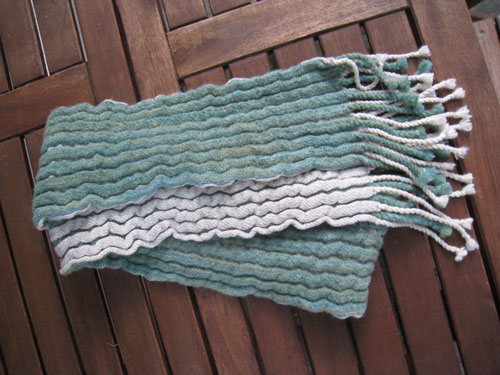
After finishing.
Here’s what the scarf looked like after a bath and a tumble in the dryer with a towel on low heat. It fulled up and shrank from 72″ on loom to 55″ fulled. I was so excited that it worked and forgot to measure it after I took it off the loom. The wavy part? Differential shrinkage between the Como (white) and the merino stripes. But I think it’s still lovely.
Next up, my own handspun cashmere pleated scarf!