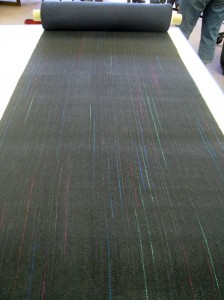
Yardage in daylight (Click to enlarge)
Here’s a picture of my yardage in daylight — just before I cut into it. I don’t have a picture of myself cutting into it. I procrastinated as long as possibly could. I love the way the fabric turned out. The color stripes remind me of a cascade of colored ashes from a fireworks display. Oh, and the actual fabric. It has absolutely gorgeous hand and drape.
After all that work on the yardage, I walked into the workshop and then dropped my jaw. It bounced a few times. I had forgotten to bring my yardage. Yes. After months and months of work, I forgot it.
I had packed the car with all the equipment, tools, and food for Daryl’s 3 day Jumpstart Jacket Workshop the night before. I left the yardage for the morning. I didn’t want to leave it in the car overnight. And the next morning? I drove away with the yardage still sitting by the front door. Sigh.
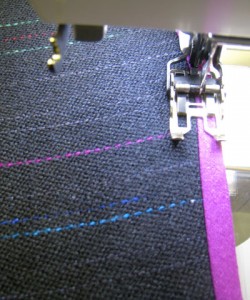
(Click to enlarge)
Okay. Onto the class. We only had 8 people in the class (instead of the typical 15). This meant that Daryl had more time to work with us individually to alter the pattern, not only for fit, but style that we want — casual, fitted, buttoned or open front, length, ease, everything. It was fabulous. Daryl was fabulous.
After all that stress about mistakes in my treadling and whether I had enough usable fabric to cut my pieces from, I had. And I have plenty to spare.
Once we got to sewing, she taught us how to apply a Hong Kong finish to all the raw edges. The finished garment will have no exposed raw edges. How fabulous is that?
I chose a fuchsia raw silk fabric from Thai Silk to make the pocket lining and bias tape from. Look how well the fuchsia matched the accent yarn.
It was a very intense 3 day workshop. I was able to finish all the major sewing by 5 PM on Sunday, but just barely. I still need to apply the bias tape to my shoulder seams. The rest of the work is handwork. I need to remove all my basting and marking stitches, hem the sleeves, and tack down the jacket hem and front band. A nice pressing and it will be done. There’s probably about another 3 hours of work remaining.

This old thing? It's just something I whipped up over the weekend.
Here’s the jacket in its current unfinished state. There are things that I would do differently, but overall, I’m very happy with how it turned out. The colored wrap threads kept it from a boring man’s suiting fabric.
Jumpstart is right. This jacket presents a great jumping off point for a lot more ideas and jackets. I’m already planning my next yardage and jacket!